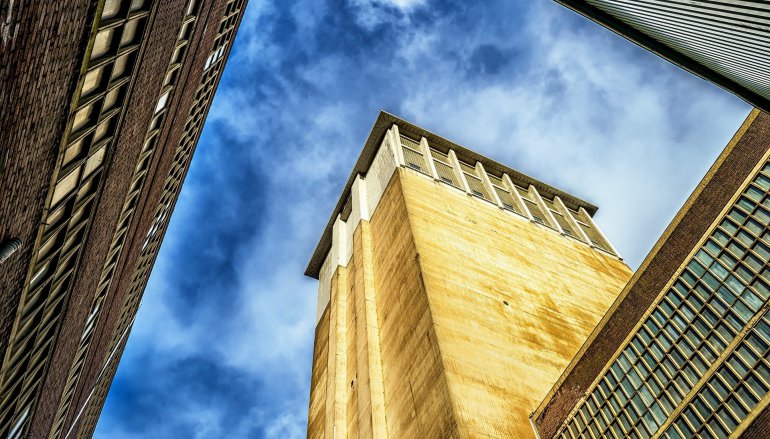
Przemysł 4.0 Technologie: Gdzie zmierza rewolucja?
Jeśli chodzi o przyswajanie nowych technologii i cyfryzację całych sektorów biznesu, nie należy szukać dalej niż rewolucja Industry 4.0. Na całym świecie firmy z branży produkcyjnej, magazynowej i logistycznej przyjmują kluczowe technologie w ramach Industry 4.0, aby otworzyć się na nowe wartości i korzyści.
Jednakże trendy w przemyśle 4.0 zmieniają się i ewoluują w miarę upływu czasu. Obecnie jest to znacznie więcej niż zwykła automatyzacja. W związku z tym chcemy przyjrzeć się technologiom i projektom w ramach Industry 4.0 w sposób bardziej szczegółowy.
Czym jest Industry 4.0?
Omówiliśmy już wcześniej temat Industry 4.0, ale oto krótkie podsumowanie. Pochodzący z Niemiec, Industry 4.0 odnosi się do czwartej Rewolucji Przemysłowej, po wprowadzeniu maszyn parowych (I Rewolucja), urządzeń elektronicznych (II Rewolucja) i początkowego wsparcia informatycznego w latach 70 (III Rewolucja).
Każda rewolucja, ze swej natury, przynosi nowe korzyści i rozwiązuje stare problemy. Jaki jest więc problem z obecnymi praktykami przemysłowymi? Cóż, tradycyjne, liniowe procesy produkcyjne wykorzystują systemy wbudowane do sterowania maszynami do różnych celów, takich jak zarządzanie prędkością linii montażowej lub sterowanie maszynami sterowanymi numerycznie (CNC), które są powszechnie używane do wykonywania określonych czynności. Takie systemy produkcyjne posiadają ograniczone dane dotyczące surowców, parametrów procesu lub produktów końcowych. Dodatkowo, wszelkie zebrane dane są okresowo analizowane, co powoduje opóźnienia w doskonaleniu procesów.
Cykl przemysłowy 4.0
Przemysł 4.0 jest poważną transformacją sposobu funkcjonowania takiej produkcji i wytwarzania. Umożliwia on przejście od procesu liniowego do integracji i dostępu do danych w czasie rzeczywistym.
Systemy cyberfizyczne - te, które integrują obliczenia cyfrowe z procesami zachodzącymi w rzeczywistości - umożliwiają gromadzenie, integrację i zaawansowaną analizę danych z maszyn i systemów danej organizacji, wykorzystując wgląd do zarządzania procesami fizycznymi. Zamiast działać reaktywnie, jak to zawsze miało miejsce, firmy mogą uczyć się po drodze i wykorzystywać wgląd do dostosowywania procesów w czasie rzeczywistym. Takie systemy mogą samodzielnie optymalizować wydajność i samodzielnie dostosowywać się do nowych warunków w podobnym tempie, uruchamiając i usprawniając całe procesy produkcyjne.
W ciągu całego cyklu dane i działania przepływają w sposób ciągły pomiędzy światem fizycznym i cyfrowym. Cykl ten składa się z trzech etapów:
- Fizyczny do cyfrowego: Tutaj firmy wychwytują informacje ze świata fizycznego i tworzą zapis cyfrowy.
- Cyfrowo do cyfrowo: Zaawansowane funkcje analityczne są wykorzystywane, często wraz z SI, do odkrywania znaczących spostrzeżeń.
- Cyfrowo do fizycznie: Przedsiębiorstwa przekładają następnie decyzje dotyczące świata cyfrowego na fizyczne działania i zmiany.
Przemysł 4.0 & IoT
Jak widać, pomost między fizycznym i cyfrowym jest niezbędny do wdrożenia w przemyśle 4.0. Do tego niezbędne są czujniki, które są w stanie dokładnie zarejestrować wszystkie potrzebne informacje.
Innymi słowy, przemysł 4.0 jest integracją Internetu przedmiotów (IoT) w ramach tych branż. Internet przedmiotów jest kluczowym czynnikiem umożliwiającym łączność, wzmacniającym technologie informatyczne, takie jak zaawansowana analiza, sztuczna inteligencja i rzeczywistość rozszerzona, co z kolei przynosi korzyści technologiom fizycznym, w tym takim jak produkcja dodatków, robotyka i zaawansowane materiały. Taka integracja umożliwia systemom fizycznym komunikację i współpracę ze sobą nawzajem, a także z pracownikami ludzkimi, działając na podstawie spostrzeżeń wynikających z zebranych danych.
Aby lepiej to opisać, w poniższej tabeli przedstawiono przykłady technologii, które są stosowane na każdym etapie pętli fizycznej do cyfrowej do fizycznej.
Digital Twin - znaczący element przemysłu 4.0
Mówiąc o technologii Industry 4.0, warto przyjrzeć się technologii Digital Twin, ponieważ jest to jedna z najnowszych i najszybciej rozwijających się technologii dostępnych dla przedsiębiorstw.
Mówiąc prościej, Digital Twin to wirtualna replika fizycznego obiektu, procesu lub produktu, która jest aktualizowana w czasie rzeczywistym. Już wcześniej zajmowaliśmy się tematem cyfrowych bliźniaków, ale wystarczy powiedzieć, że mogą one obejmować zarówno pojedynczy element wyposażenia, jak i całą linię produkcyjną. Cyfrowy bliźniak łączy dane z różnych źródeł, takich jak pomiary danych w czasie rzeczywistym z czujników IoT, metadane, projekty CAD, raporty i dokumentacja tworzona w trakcie cyklu życia obiektu. Firmy mogą wykorzystywać te dane do przeprowadzania symulacji procesów, reagowania w czasie rzeczywistym na zmiany parametrów, aby zapobiegać przestojom, zarządzać procesami produkcyjnymi, optymalizować zapasy dostaw i nie tylko.
W wyżej wspomnianej pętli fizyczno-cyfrowo-fizycznej, A Digital Twin jest kluczowym ogniwem łączącym świat fizyczny i cyfrowy. W połączeniu z nowoczesną masową mocą obliczeniową i zaawansowanymi algorytmami analizy w czasie rzeczywistym umożliwiają one fundamentalne zmiany projektowe i procesowe, które prawie na pewno byłyby nieosiągalne za pomocą obecnych metod.
Kto korzysta z technologii Digital Twin?
Cyfrowe bliźniaki mogą być tworzone dla różnych zasobów, aby służyły różnym celom. Jednym z przykładów może być wirtualna replika pojedynczej maszyny w ramach linii produkcyjnej, stworzona w celu monitorowania i optymalizacji wydajności pojedynczego składnika aktywów.
Jednak pełny potencjał i wartość biznesowa Digital Twin zostają odblokowane podczas łączenia różnych replik w ramach określonego procesu, w którym Digital Twins pojedynczych aktywów oddziałuje na siebie. Tutaj mogą one wymieniać dane między sobą i uzyskać pełny obraz procesu i zależności między poszczególnymi etapami. Wszystko to pozwala na nowe przypadki wykorzystania, a także na znaczne usprawnienie procesu.
Jak branża 4.0 tworzy wartość
Dzięki cyfryzacji operacji, produkcji, łańcuchów dostaw i produktów, firmy mogą łączyć unikalną wiedzę i korzyści płynące z ludzi, maszyn, analizy i przewidywania, aby podejmować lepsze decyzje, co ostatecznie prowadzi do dodatkowej wartości dla biznesu.
Patrząc konkretnie na branżę 4.0 w produkcji, McKinsey zidentyfikował osiem głównych czynników wartości, które mają wpływ na wyniki firmy. Stwierdzili oni, że zastosowanie Branży 4.0 w odniesieniu do każdego z tych czynników wartości dodanej prowadzi do zauważalnej poprawy.
Mając to na uwadze, przyjrzyjmy się bliżej każdemu z nich.
Zasoby/procesy - mechanizmy branżowe 4.0 poprawiają efektywność procesów produkcyjnych. Na przykład ABB zastosowała system komputerowy do kontroli i optymalizacji jednej z operacji pieca do wypalania cementu u swojego klienta. System ten naśladuje zachowanie "idealnego" operatora cementowni. Wykorzystuje on rzeczywiste środki do obliczania parametrów procesu wymaganych do osiągnięcia docelowej wydajności i dostosowuje odpowiedni proces w czasie rzeczywistym. W wyniku tego wydajność wzrosła o 5%.
Wykorzystanie zasobów - Rozwiązania branżowe 4.0, takie jak konserwacja zapobiegawcza, mogą zapewnić wartość dodaną poprzez skrócenie czasu przestoju maszyny lub czasu przezbrojenia. GE10 oferuje konserwację prognostyczną, w ramach której czujniki IoT zbierają i raportują dane na temat stanu odpowiednich maszyn. Zaawansowane rozwiązania analityczne wykorzystują te dane do wykrywania wczesnych oznak różnych problemów, wskazując, które maszyny wymagają lub będą wymagały konserwacji. Konserwacja prognostyczna może skrócić czas przestoju maszyny o 30-50%, a także zwiększyć jej żywotność o 20-40%.
Poprawa wydajności pracy - Przemysł 4.0 wnosi wartość dodaną poprzez skrócenie czasu oczekiwania lub po prostu zwiększenie szybkości działania. Na przykład, możemy przyjrzeć się firmie Etalex, producentowi mebli magazynowych, który wprowadził roboty w celu zwiększenia wydajności pracy. Roboty te są wykorzystywane do wspomagania pracowników firmy w wykonywaniu zadań wymagających wysiłku fizycznego. W rezultacie, ta współpraca człowieka z robotem zwiększyła wydajność o 40% bez zwiększania bazy pracowników.
Optymalizacja zapasów - Ta jest dość prosta, ale korzyści są równie zdumiewające. W obudowie iBins firmy Wurth w wersji 4.0, przeznaczonej do użytku w przemyśle, zastosowano inteligentne kamery do monitorowania poziomu zapełnienia skrzynek z zapasami. Każda skrzynka automatycznie zmienia kolejność napełniania w oparciu o dokładne dane. Taka optymalizacja zaopatrzenia w czasie rzeczywistym pozwoliła obniżyć koszty zapasów o 20-50%.
Poprawa jakości - Toyota wykorzystuje zaawansowane narzędzia kontroli procesów i analizy danych do śledzenia i korygowania błędów w czasie rzeczywistym. Dzięki tym działaniom udało się zminimalizować ilość wymaganych przeróbek, jak również generowanych odpadów. Zastosowanie systemu Industry 4.0 pozwala obniżyć koszty związane z nieoptymalną jakością nawet o 20%.
Dopasowanie podaży do popytu - Aby zmaksymalizować wartość uzyskaną z rynku, każda firma musi zrozumieć wymagania swoich klientów. Industry 4.0 daje firmom narzędzia i środki do pełnego wykorzystania ich potencjału. Producenci oryginalnego wyposażenia w sektorze motoryzacyjnym, na przykład, używają narzędzi konfiguracyjnych online do identyfikacji produktów i opcji, za które klienci są gotowi zapłacić. Takie rozwiązania pomagają firmom usuwać niechciane opcje, koncentrując się tylko na tym, czego szukają klienci. W rezultacie czas i koszty produkcji zostają zredukowane, ponieważ całkowicie eliminuje się niepotrzebne opcje.
Czas na wprowadzenie na rynek - Krótki czas na wprowadzenie na rynek daje dużą przewagę podmiotom, które jako pierwsze weszły na rynek, a podmioty z branży 4.0 mogą pomóc w przyspieszeniu procesu rozwoju. Firma Local Motors produkuje na przykład samochody w technologii druku 3D, a projekty pochodzą od społeczności internetowej. Dzięki tym innowacjom firma jest w stanie skrócić cykl rozwoju z sześciu lat - średniej w branży - do zaledwie jednego roku. Dodatkowo, udało im się osiągnąć znaczną redukcję kosztów badań i rozwoju. Według McKinsey'a, możliwy czas redukcji może wynieść od 30-50%.
Serwis/sprzedaż posprzedażna - Konserwacja i naprawy są ważnymi czynnikami wpływającymi na koszty serwisu, więc oczywiście obniżenie tych kosztów dla klienta otwiera potencjał do tworzenia dodatkowej wartości. Secomea, na przykład, wykorzystuje zdalną konserwację do świadczenia usług serwisowych dla swoich klientów. Firma korzysta z oprogramowania, które umożliwia technikom nawiązywanie zdalnych połączeń z urządzeniami przemysłowymi w siedzibie klienta i przeprowadzanie diagnostyki. Zdalna i predykcyjna konserwacja, o której już wspominaliśmy, może zmniejszyć koszty konserwacji o 10-40%.
Inne technologie i tendencje rynkowe
Oczywiście, nie chodzi tylko o Digital Twin. Istnieje cała gama rozwiązań do wyboru, a wiele z tych branżowych technologii 4.0 również się rozwija. Oto niektóre z największych trendów w przemyśle 4.0, których należy być świadomym.
Ponad 50% aktywów przemysłowych w fabrykach zostanie podłączonych.
Przemysł 4.0 nie jest pojęciem teoretycznym, lecz rzeczywistym trendem wpływającym na sposób funkcjonowania przedsiębiorstw. Coraz większa liczba producentów buduje rozwiązania w zakresie gromadzenia danych przemysłowych. Według raportu IoT Analytics, do 2020 roku ponad 50% aktywów przemysłowych zostanie podłączonych do pewnego rodzaju systemu gromadzenia danych. Odsetek podłączonych aktywów będzie tylko wzrastał i ma być kluczowym motorem wzrostu rynku łączności przemysłowej.
Łączność Edge-To-Cloud
W ciągu ostatnich kilku lat systemy Enterprise Resource Planning (ERP), Manufacturing Execution System (MES) oraz Supervisory Control And Data Acquisition (SCADA) zostały przeniesione do Cloud. W związku z tym pojawiły się nowe architektury łączności, umożliwiające bezpośrednie połączenie z chmurą. Tam, gdzie tradycyjna komunikacja poprzez systemy SCADA i MES zależy od serwerów Open Platform Communications (OPC), postęp w technologii łączności (protokoły łączności), sprzęt komputerowy (tanie komputery typu edge computing, które mogą uruchamiać aplikacje i umożliwiać łączność typu edge-to-cloud) oraz oprogramowanie (oprogramowanie zaprojektowane do pracy na urządzeniach typu edge, tak małych jak Raspberry Pi) umożliwiają tworzenie nowych architektur, w których urządzenia typu edge mogą nawiązywać bezpośrednie połączenie z Cloud.
Obliczenia krawędziowe
W ostatnich latach informatyka korporacyjna staje się coraz bardziej chmurowa, co ma wiele powodów. Rozwiązania w chmurze są często tańsze i bardziej wydajne, a także łatwiejsze do wdrożenia, utrzymania i skalowania. Przechowywanie danych na scentralizowanym, ale łatwo dostępnym serwerze poza siedzibą przedsiębiorstwa ułatwia współpracę, umożliwia zdalną pracę i znacznie zwiększa elastyczność.
Jednak potrzeby biznesowe zmieniają się. Pojawienie się 5G i rosnąca popularność IoT spowodowały, że obok analizy w czasie rzeczywistym powstają duże ilości danych. W konsekwencji, przedsiębiorstwa poszukują alternatywnych rozwiązań obliczeniowych. Pomimo wielu zalet chmury, opóźnienie hostowanych rozwiązań jest często niewystarczające dla niektórych przypadków zastosowań w branży 4.0. Jak wspomniano wcześniej, znaczna część Industry 4.0 bada ocenę danych z prędkością, często z reakcjami w czasie zbliżonym do rzeczywistego. W sytuacjach takich jak ta, dodatkowe milisekundy opóźnienia na jedno działanie mogą ostatecznie spowodować zauważalne wgniecenie w idealnej poprawie.
W przypadku przetwarzania danych w czasie krytycznym użytkownicy przesuwają się w kierunku obliczeń krawędziowych, co powoduje, że przechowywanie i przetwarzanie danych jest bliżej miejsca, w którym są one potrzebne. Umieszczenie mocy obliczeniowej jak najbliżej czujników przechwytujących dane, o których mowa, zmniejsza ilość danych przesyłanych do chmury, co upraszcza bezpieczeństwo i skraca czas reakcji sieci.
Zwiększona popularność AI i Advanced Analytics
Zaawansowana analityka i sztuczne inteligencje stają się coraz bardziej wydajne, a także coraz bardziej opłacalne do wykorzystania przez firmy. Rozwiązania w chmurze i inne udoskonalone możliwości obliczeniowe sprawiają, że technologie te stają się bardziej dostępne. Wiele firm zdało sobie już sprawę, że zaawansowana analityka i sztuczna inteligencja mogą tworzyć znaczącą wartość, gdy są stosowane w przemyśle wytwórczym. Przykładem może być konserwacja prognostyczna, cyfrowe zarządzanie jakością oraz prognozowanie popytu wywołanego sztuczną inteligencją. Sztuczna inteligencja odgrywa kluczową rolę w inteligentnej fabryce, pomagając producentom przewidywać popyt i przydzielać zasoby.
Podsumowanie
Branża 4.0 nie jest już tylko pojęciem, nie chodzi też "tylko" o cyfryzację danych. Jest to cała rewolucja technologiczna, która obejmuje technologie Internetu przedmiotów, wielkich danych, analizy i uczenia się maszyn, aby stworzyć nowe możliwości i korzyści, które po prostu nie były dostępne bez takiej technologii.
Perspektywa biznesowa
Przemysł 4.0 stanowi szansę dla tradycyjnych gałęzi przemysłu, takich jak produkcja, na cyfryzację swojej działalności w celu uzyskania nowych korzyści. Rozwiązania cyfrowe mogą szybko ocenić dane, obniżyć koszty i zoptymalizować procesy. Na rynkach, na których nawet niewielkie optymalizacje znacznie różnią się od siebie w produkcji na dużą skalę lub po prostu pomagają wyprzedzić konkurencję, przemysł 4.0 nie jest opcją, lecz coraz bardziej wymagającą inwestycją.
Zobacz również
Komentarze (0)
VWinyle powróciły w ostatnich latach, ale aby zbudować system hi-fi wokół Twojego odtwarzacza płyt, może być trudno wiedzieć, od czego zacząć. "Dla mnie chodzi o całe to wydarzenie, które składa się na album" - mówi Sam Smith, inżynier elektroniki w Cambridge Audio...
VJakość kabla może mieć znaczenie jeśli chodzi o odtwarzanie dźwięku. Kiedy jakość kabla nie wpływa na dźwięk? Chociaż prawdą jest, że wiele elementów i przewodników elektrycznych ma pojemność i indukcyjność, które mogą wpływać na dźwięk, przewód głośnikowy ma ich...
Jak mobilne uczenie się rewolucjonizuje edukację
VTechnologia mobilna wkroczyła we wszystkie sfery współczesnego życia, w tym w dziedzinę edukacji. Cyfrowe tablice, wirtualne fora dyskusyjne i interaktywne podręczniki zasilane urządzeniami mobilnymi stały się już nieodłączną częścią procesu edukacyjnego dla wielu instytucji...
Zostaw komentarz